ප්ලාස්ටික් කොටස් සැලසුම් කරන්නේ කෙසේද
කෙටි විස්තරය:
දක්වා ප්ලාස්ටික් කොටස් සැලසුම් කරන්නනිෂ්පාදනයේ කොටස් ඉටු කරන කාර්යභාරය සහ ප්ලාස්ටික් සඳහා අච්චු සැකසීමේ රීතිය මත පදනම්ව කොටස්වල හැඩය, ප්රමාණය සහ නිරවද්යතාවය නිර්වචනය කිරීමයි. අවසාන නිමැවුම වන්නේ අච්චුව සහ ප්ලාස්ටික් කොටස නිෂ්පාදනය සඳහා ඇඳීම් ය.
නිෂ්පාදන නිෂ්පාදනය ආරම්භ වන්නේ සැලසුමෙනි. ප්ලාස්ටික් කොටස් සැලසුම් කිරීම නිෂ්පාදනයේ අභ්යන්තර ව්යුහය, පිරිවැය සහ ක්රියාකාරිත්වය සාක්ෂාත් කර ගැනීම සෘජුවම තීරණය කරන අතර අච්චු නිෂ්පාදනයේ ඊළඟ පියවර, පිරිවැය සහ චක්රය මෙන්ම එන්නත් අච්චු සැකසීම සහ පශ්චාත් සැකසුම් ක්රියාවලිය සහ පිරිවැය ද තීරණය කරයි.
නූතන සමාජයේ විවිධ නිෂ්පාදන, පහසුකම් සහ ජනතාවගේ ජීවිතවල ප්ලාස්ටික් කොටස් බහුලව භාවිතා වේ. ප්ලාස්ටික් කොටස් වලට විවිධ හැඩයන් සහ කාර්යයන් අවශ්ය වේ. ඔවුන් ප්ලාස්ටික් ද්රව්ය භාවිතා කරන අතර ඒවායේ ගුණාංග විවිධ වේ. ඒ අතරම, කර්මාන්තයේ ප්ලාස්ටික් කොටස් සෑදීමට බොහෝ ක්රම තිබේ. එබැවින් ප්ලාස්ටික් කොටස් සැලසුම් කිරීම සරල කාර්යයක් නොවේ.
විවිධ කොටස් සැකසීම සහ ද්රව්ය විවිධ සැකසුම් වලින් නිපදවනු ලැබේ. ප්ලාස්ටික් සැකසීම සඳහා සැකසුම් කිරීම ප්රධාන වශයෙන් පහත දැක්වේ:
1.injection මෝල්ඩින්
අච්චු ගැසීම
3. සම්පීඩන අච්චුව
4.රොටේෂන් අච්චුව
5. තාප සැකැස්ම
6.extrusion
7. පිරිසැකසුම් කිරීම
8. ෆෝමිං
මහා පරිමාණයෙන් ඒවා නිෂ්පාදනය කිරීමට ක්රම ගණනාවක් තිබේ. ඉන්ජෙක්ෂන් මෝල්ඩින් කිරීම ජනප්රිය නිෂ්පාදන ක්රමයක් වන අතර ඉන්ජෙක්ෂන් අච්චු 50% ~ 60% ප්ලාස්ටික් කොටස් නිපදවන්නේ බීබී ඉන්ජෙක්ෂන් මෝල්ඩින් නිසා එය අධිවේගී නිෂ්පාදන හැකියාවකි.
අප විසින් නිර්මාණය කරන ලද සමහර ප්ලාස්ටික් කොටස් සඳහා නඩුව පෙන්වන්න:
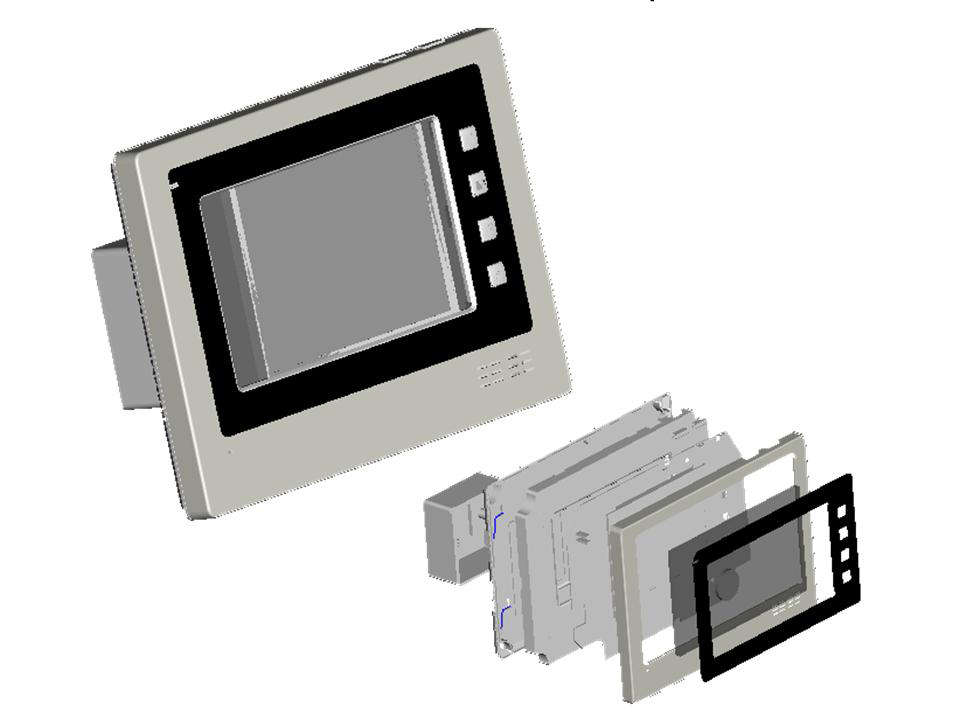
දර්ශන දුරකථනයේ ප්ලාස්ටික් කොටු කිරීම
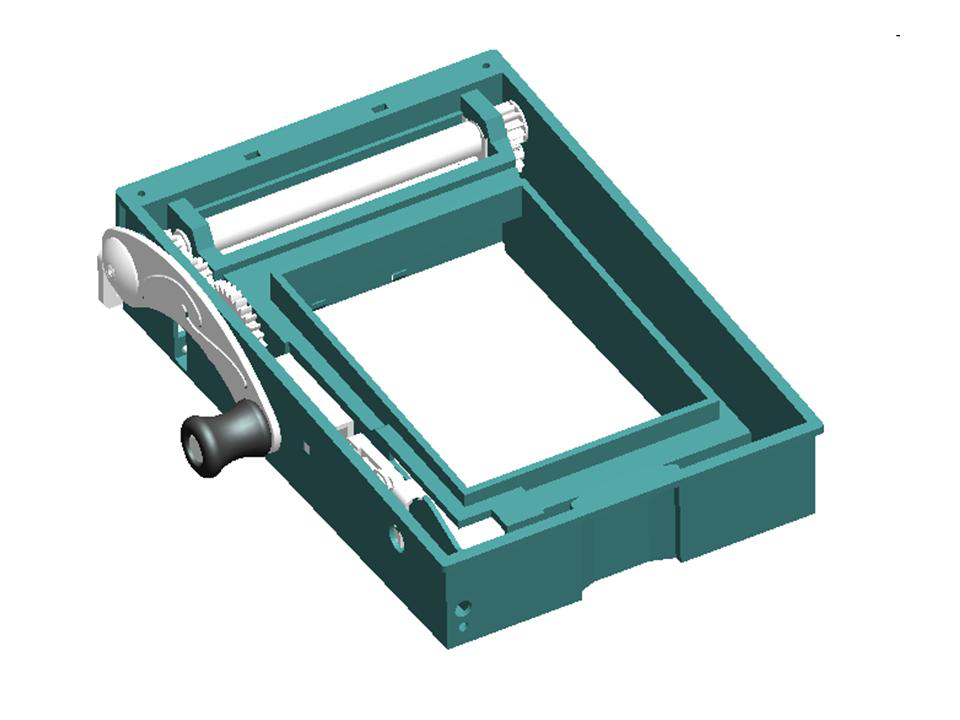
යාන්ත්රණයේ ප්ලාස්ටික් කොටස්
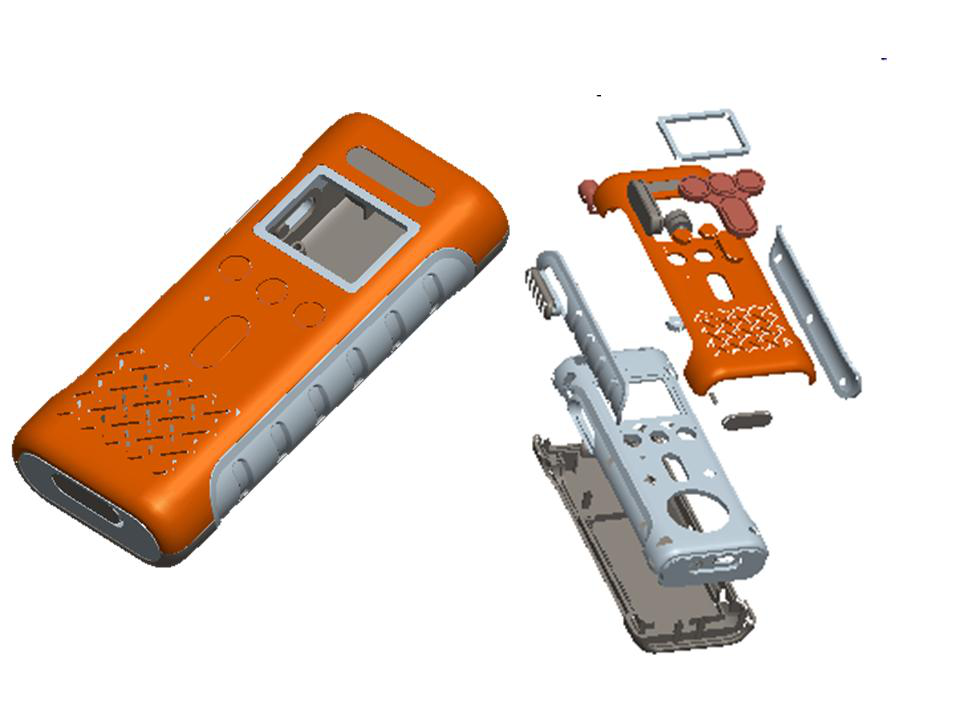
ඉලෙක්ට්රොනික ප්ලාස්ටික් නඩු
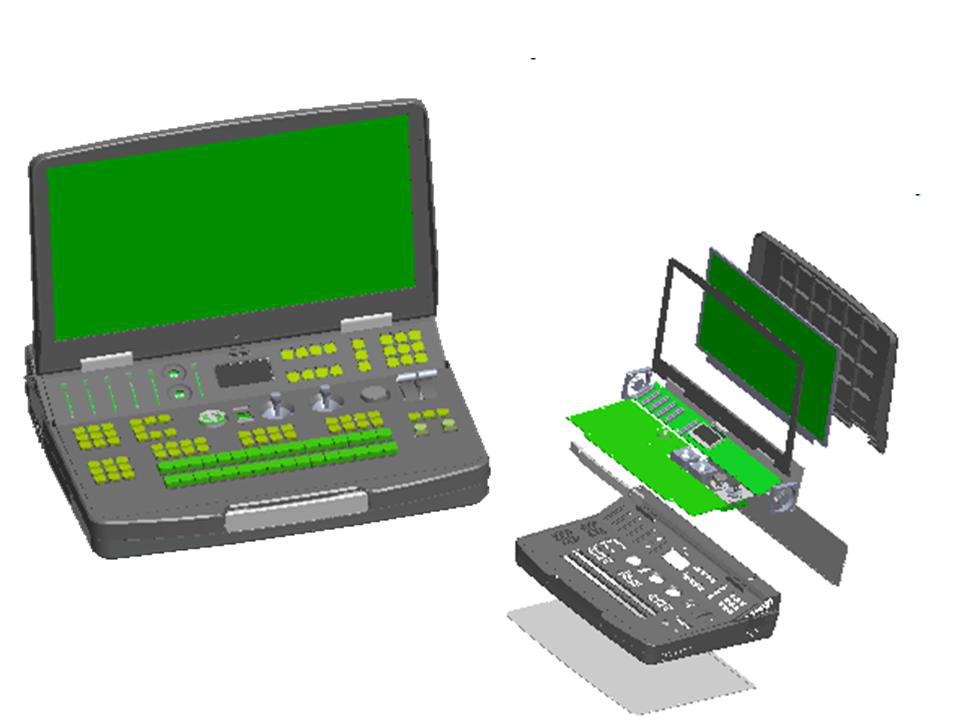
උපකරණ සඳහා ප්ලාස්ටික් නිවාස
අංශ තුනකින් ප්ලාස්ටික් කොටස් සැලසුම් කරන්නේ කෙසේද යන්න අපි විස්තරාත්මකව බෙදා ගනිමු
* ඔබ දැන සිටිය යුතු ප්ලාස්ටික් කොටස් සැලසුම් කිරීම සඳහා උපදෙස් 10 ක්
1. නිෂ්පාදනයේ පෙනුම සහ ප්රමාණය තීරණය කරන්න.
සමස්ත සැලසුම් ක්රියාවලියේ පළමු පියවර මෙයයි. වෙළඳපල පර්යේෂණ සහ පාරිභෝගික අවශ්යතා අනුව, නිෂ්පාදනවල පෙනුම සහ ක්රියාකාරිත්වය තීරණය කිරීම සහ නිෂ්පාදන සංවර්ධන කාර්යයන් සකස් කිරීම.
සංවර්ධන කර්තව්යයට අනුව, සංවර්ධන කණ්ඩායම විසින් නිෂ්පාදනයට තාක්ෂණික හා තාක්ෂණික ශක්යතා විශ්ලේෂණය සිදු කරන අතර නිෂ්පාදනයේ ත්රිමාණ පෙනුම ආකෘතිය ගොඩනංවයි. එවිට, ක්රියාකාරී අවබෝධය සහ නිෂ්පාදන එකලස් කිරීම අනුව, හැකි කොටස් සැලසුම් කර ඇත.
නිෂ්පාදන චිත්ර වලින් තනි කොටස් වෙන් කරන්න, ප්ලාස්ටික් කොටස් සඳහා ප්ලාස්ටික් ෙරසින් වර්ගය තෝරන්න
මෙම පියවර වන්නේ පෙර පියවරේදී ලබාගත් ත්රිමාණ ආකෘතියෙන් කොටස් වෙන් කොට ඒවා තනි තනිව නිර්මාණය කිරීමයි. කොටස්වල ක්රියාකාරී අවශ්යතා අනුව සුදුසු ප්ලාස්ටික් අමුද්රව්ය හෝ දෘඩාංග ද්රව්ය තෝරන්න. උදාහරණයක් ලෙස, ABS සාමාන්යයෙන් භාවිතා වන්නේ
ෂෙල්, ඒබීඑස් / බීසී හෝ පීසී වලට යම් යාන්ත්රික ගුණාංග, ලාම්පු ෂේඩ්, ලාම්පු පෝස්ට් පීඑම්එම්ඒ හෝ පීසී වැනි විනිවිද පෙනෙන කොටස්, ගියර් හෝ පළඳින කොටස් POM හෝ නයිලෝන් තිබිය යුතුය.
කොටස්වල ද්රව්ය තෝරා ගැනීමෙන් පසුව, සවිස්තරාත්මක සැලසුම ආරම්භ කළ හැකිය.
3. කෙටුම්පත් කෝණ නිර්වචනය කරන්න
කෙටුම්පත් කෝණ මඟින් අච්චුවෙන් ප්ලාස්ටික් ඉවත් කිරීමට ඉඩ ලබා දේ. කෙටුම්පත් කෝණ නොමැතිව, කොටස ඉවත් කිරීමේදී iction ර්ෂණය හේතුවෙන් සැලකිය යුතු ප්රතිරෝධයක් ලබා දෙනු ඇත. කෙටුම්පත් කෝණ කොටසේ ඇතුළත හා පිටත තිබිය යුතුය. ගැඹුරු කොටස, කෙටුම්පත් කෝණය විශාල වේ. සරල රීතියක් නම් අඟලකට අංශක 1 ක කෙටුම්පත් කෝණයක් තිබීමයි. ප්රමාණවත් කෙටුම්පත් කෝණයක් නොතිබීම නිසා කොටසේ දෙපැත්තේ සීරීම් සහ / හෝ විශාල ඉෙජෙක්ටර් පින් ලකුණු ඇති විය හැක (මේ ගැන පසුව වැඩි විස්තර).
පිටත පෘෂ් of යේ කෙටුම්පත් කෝණ: ගැඹුරු කොටස, කෙටුම්පත් කෝණය විශාල වේ. සරල රීතියක් නම් අඟලකට අංශක 1 ක කෙටුම්පත් කෝණයක් තිබීමයි. ප්රමාණවත් කෙටුම්පත් කෝණයක් නොතිබීම නිසා කොටසේ දෙපැත්තේ සීරීම් සහ / හෝ විශාල ඉෙජෙක්ටර් පින් ලකුණු ඇති විය හැක (මේ ගැන පසුව වැඩි විස්තර).
සාමාන්යයෙන්, හොඳ පෙනුමක් ඇති පෘෂ් have යක් ලබා ගැනීම සඳහා, වයනය කොටස් මතුපිට සකස් කර ඇත. වයනය සහිත බිත්තිය රළු ය, iction ර්ෂණය විශාල වන අතර එය කුහරයෙන් ඉවත් කිරීම පහසු නැත, එබැවින් එයට විශාල ඇඳීමේ කෝණයක් අවශ්ය වේ. ගොරෝසු වයනය නම්, විශාල කෙටුම්පත් කෝණය අවශ්ය වේ.
බිත්ති thickness ණකම / ඒකාකාර .ණකම නිර්වචනය කරන්න
පහත සඳහන් හේතූන් නිසා එන්නත් අච්චු කිරීමේදී shape න හැඩ හැඩගැන්වීම අවශ්ය නොවේ:
1). සිසිලන කාලය බිත්ති .ණකම වර්ගයට සමානුපාතික වේ. Solid න සඳහා දිගු සිසිලන කාලය මහා නිෂ්පාදනයේ ආර්ථිකය පරාජය කරනු ඇත. (තාපයේ දුර්වල සන්නායකය)
2) .ටිකර් කොටස තුනී කොටසට වඩා හැකිලී, එමඟින් යුධ පිටුවක් හෝ බේසම සලකුණු ආදියෙහි අවකල්ය හැකිලීමක් හඳුන්වා දෙයි (ප්ලාස්ටික් හා පීවීටී ලක්ෂණ වල හැකිලීමේ ලක්ෂණ)
එබැවින් ප්ලාස්ටික් කොටස් සැලසුම් කිරීම සඳහා අපට මූලික රීතියක් ඇත; හැකිතාක් දුරට බිත්ති thickness ණකම කොටස හරහා ඒකාකාර හෝ නියත විය යුතුය. මෙම බිත්ති thickness ණකම නාමික බිත්ති .ණකම ලෙස හැඳින්වේ.
කොටසෙහි කිසියම් section න අංශයක් තිබේ නම්, හරය හඳුන්වා දීමෙන් එය කුහරයක් බවට පත් කළ යුතුය. මෙය හරය වටා ඒකාකාර බිත්ති thickness ණකම සහතික කළ යුතුය.
3). බිත්ති thickness ණකම තීරණය කිරීම සඳහා සලකා බැලිය යුතු කරුණු මොනවාද?
එය කාර්යය සඳහා thick න සහ තදින් තිබිය යුතුය. බිත්ති thickness ණකම 0.5 සිට 5mm විය හැකිය.
වේගයෙන් සිසිල් වීමට තරම් සිහින් විය යුතු අතර එහි ප්රති lower ලයක් ලෙස අඩු බර හා ඉහළ tivity ලදායිතාව ඇත.
බිත්ති thickness ණකමෙහි ඕනෑම වෙනසක් හැකිතාක් අවම වශයෙන් තබා ගත යුතුය.
විවිධ බිත්ති thickness ණකම සහිත ප්ලාස්ටික් කොටසකට වෙනස් සිසිලන අනුපාත සහ විවිධ හැකිලීම් අත්විඳිය හැකිය. එවැනි අවස්ථාවකදී සමීප ඉවසීමක් ලබා ගැනීම ඉතා අපහසු වන අතර බොහෝ වාරයක් කළ නොහැකි ය. බිත්ති thickness ණකම විචලනය අත්යවශ්ය වන විට, දෙක අතර සංක්රාන්තිය ක්රමයෙන් විය යුතුය.
5. කොටස් අතර සම්බන්ධතා සැලසුම
සාමාන්යයෙන් අපි ෂෙල් වෙඩි දෙකක් එකට සම්බන්ධ කළ යුතුයි. අභ්යන්තර සංරචක (PCB එකලස් කිරීම හෝ යාන්ත්රණය) ස්ථානගත කිරීම සඳහා ඔවුන් අතර සංවෘත කාමරයක් සැකසීම.
සුපුරුදු සම්බන්ධතා වර්ග:
1). කොකු කඩා දමන්න:
කුඩා හා මධ්යම ප්රමාණයේ නිෂ්පාදන සඳහා Snap කොකු සම්බන්ධතාවය බහුලව භාවිතා වේ. එහි ලක්ෂණය වන්නේ සාමාන්යයෙන් කොකු සවි කර ඇත්තේ කොටස් අද්දර වන අතර නිෂ්පාදන ප්රමාණය කුඩා කළ හැකිය. එකලස් කරන විට, ඉස්කුරුප්පු නියන, අතිධ්වනික වෙල්ඩින් ඩයි සහ වෙනත් මෙවලම් භාවිතා නොකර එය සෘජුවම වසා ඇත. අවාසිය නම්, හදිසි කොකු අච්චුව වඩාත් සංකීර්ණ වීමට හේතු විය හැක. ස්නැප් කොකු සම්බන්ධතාවය අවබෝධ කර ගැනීමට සහ අච්චු පිරිවැය වැඩි කිරීමට ස්ලයිඩර් යාන්ත්රණය සහ එසවුම් යාන්ත්රණය අවශ්ය වේ.
2). ඉස්කුරුප්පු සන්ධි:
ඉස්කුරුප්පු සන්ධි ස්ථීර හා විශ්වාසදායකය. විශේෂයෙන්, ඉස්කුරුප්පු + නට් සවි කිරීම ඉතා විශ්වාසදායක හා කල් පවතින අතර ඉරිතැලීම් නොමැතිව බහු විසුරුවා හැරීමට ඉඩ සලසයි. ඉස්කුරුප්පු සම්බන්ධතාවය විශාල අගුලු දැමීමේ බලය සහ බහු විසුරුවා හැරීම් සහිත නිෂ්පාදන සඳහා සුදුසු වේ. අවාසිය නම් ඉස්කුරුප්පු තීරුවට වැඩි ඉඩක් ගැනීමයි.
3). සවිකරන ලොක්කන්:
ලොක්කන්ගේ සම්බන්ධතාවය සවි කිරීම යනු ලොක්කන් සහ සිදුරු අතර දැඩි සම්බන්ධීකරණයෙන් කොටස් දෙකක් සවි කිරීමයි. නිෂ්පාදන විසුරුවා හැරීමට ඉඩ දීමට තරම් මෙම සම්බන්ධතාවය ශක්තිමත් නොවේ. අවාසිය නම්, විසුරුවා හැරීමේ කාලය වැඩි වන විට අගුලු දැමීමේ ශක්තිය අඩු වීමයි.
4). අතිධ්වනික වෙල්ඩින්:
අතිධ්වනික වෑල්ඩින් යනු අතිධ්වනික වෙල්ඩින් යන්ත්රයේ ක්රියාකාරිත්වය යටතේ කොටස් දෙක අතිධ්වනික අච්චුව තුළට දමා ස්පර්ශක මතුපිට විලයනය කිරීමයි. නිෂ්පාදන ප්රමාණය කුඩා විය හැකිය, එන්නත් කිරීමේ අච්චුව සාපේක්ෂව සරල වන අතර සම්බන්ධතාවය ස්ථිරයි. අවාසිය නම් අතිධ්වනික අච්චුව සහ අතිධ්වනික වෙල්ඩින් යන්ත්රය භාවිතා කිරීමයි, නිෂ්පාදන ප්රමාණය විශාල විය නොහැක. විසුරුවා හැරීමෙන් පසු අතිධ්වනික කොටස් නැවත භාවිතා කළ නොහැක.
6.අන්ඩර්කට්
යටි කප්පාදුව යනු අච්චුවෙන් අඩක් ඉවත් කිරීමට බාධා කරන අයිතම වේ. මෝස්තරයේ ඕනෑම තැනක යටි කප්පාදුවක් දිස්විය හැකිය. කෙටුම්පත් කෝණයක lack නතාවයට වඩා නරක නොවේ නම් මේවා පිළිගත නොහැකිය. කෙසේ වෙතත්, සමහර යටි පතුල් අවශ්ය සහ / හෝ වැළැක්විය නොහැක. එවැනි අවස්ථාවන්හිදී, අවශ්ය වේ
යටි අච්චු නිපදවන්නේ අච්චුවේ කොටස් ලිස්සා යාම / චලනය කිරීමෙනි.
අච්චුව නිපදවීමේදී යටි පතුල් සෑදීම වඩා මිල අධික වන අතර එය අවම මට්ටමක තබා ගත යුතු බව මතක තබා ගන්න.
7. ආධාරක ඉළ ඇට / ගුසෙට්ස්
ප්ලාස්ටික් කොටසෙහි ඉළ ඇට කොටසෙහි තද බව (බර හා අර්ධ අපගමනය අතර සම්බන්ධතාවය) වැඩි දියුණු කරන අතර දෘඩතාව වැඩි කරයි. ඉළ ඇටයේ දිශාවට දියවන ප්රවාහය වේගවත් කරන බැවින් එය අච්චු හැකියාව වැඩි කරයි.
ඉළ ඇට උපරිම ආතතිය හා දිශාවට නොපෙනී යන පෘෂ් on යන් මත තබා ඇත. පුස් පිරවීම, හැකිලීම සහ පිට කිරීම ද ඉළ ඇට ස්ථානගත කිරීමේ තීරණ කෙරෙහි බලපෑම් කළ යුතුය.
සිරස් බිත්තියට සම්බන්ධ නොවන ඉළ ඇට හදිසියේම අවසන් නොවිය යුතුය. නාමික බිත්තියට ක්රමයෙන් මාරුවීම ආතතිය සාන්ද්රණය සඳහා ඇති අවදානම අඩු කළ යුතුය.
ඉළ ඇට - මානයන්
ඉළ ඇට පහත මානයන් තිබිය යුතුය.
සින්ක් සලකුණ වළක්වා ගැනීම සඳහා ඉළ ඇටයේ thickness ණකම නාමික බිත්ති thickness ණකම 0.5 සිට 0.6 ගුණයක් විය යුතුය.
ඉළ ඇටයේ උස නාමික බිත්ති .ණකම 2.5 සිට 3 ගුණයක් විය යුතුය.
ඉදිමීම පහසු කිරීම සඳහා රිබ් අංශක 0.5 සිට 1.5 දක්වා කෙටුම්පත් කෝණයක් තිබිය යුතුය.
ඉළ ඇටයේ නාමික බිත්ති .ණකම 0.25 සිට 0.4 ගුණයක් විය යුතුය.
ඉළ ඇට දෙකක් අතර දුර නාමික බිත්ති .ණකම 2 සිට 3 ගුණයක් (හෝ ඊට වැඩි) විය යුතුය.
8. විකිරණශීලී දාර
පෘෂ් two දෙකක් හමු වූ විට, එය කෙළවරක් සාදයි. කෙළවරේ බිත්ති thickness ණකම නාමික බිත්ති .ණකම මෙන් 1.4 ගුණයක් දක්වා වැඩිවේ. මෙහි ප්රති results ලය වන්නේ අවකල්ය හැකිලීම සහ අච්චු ගැසූ ආතතිය සහ දිගු සිසිලන කාලයයි. එබැවින්, සේවාව අසාර්ථක වීමේ අවදානම තියුණු කොන් වලින් වැඩි වේ.
මෙම ගැටළුව විසඳීම සඳහා, කොන් අරය සමඟ සුමට කළ යුතුය. අරය බාහිරව මෙන්ම අභ්යන්තරවද සැපයිය යුතුය. ඉරිතැලීම් ප්රවර්ධනය කරන බැවින් කිසි විටෙකත් අභ්යන්තර තියුණු කොනක් නොතබන්න. අරය නියත බිත්ති thickness ණකම රීතියට සනාථ වන පරිදි විය යුතුය. කොන් වල බිත්ති thickness ණකම 0.6 සිට 0.75 ගුණයක් අරය තිබීම වඩාත් සුදුසුය. ඉරිතැලීම් ප්රවර්ධනය කරන බැවින් කිසි විටෙකත් අභ්යන්තර තියුණු කොනක් නොතිබිය යුතුය.
9. ඉස්කුරුප්පු ලොක්කා නිර්මාණය
අපි සෑම විටම අර්ධ නඩු දෙකක් නිවැරදි කිරීමට ඉස්කුරුප්පු භාවිතා කරමු, නැතහොත් PCBA හෝ වෙනත් සංරචක ප්ලාස්ටික් කොටස් මත සවි කරන්න. එබැවින් ඉස්කුරුප්පු ලොක්කන් යනු ඉස්කුරුප්පු ඇණ සහ ස්ථාවර කොටස් සඳහා ව්යුහයයි.
ඉස්කුරුප්පු ලොක්කා සිලින්ඩරාකාර හැඩයෙන් යුක්තය. ලොක්කා මූලික වශයෙන් මවගේ කොටස සමඟ සම්බන්ධ කළ හැකිය, නැතහොත් එය පැත්තකින් සම්බන්ධ කළ හැකිය. පැත්තේ සම්බන්ධ වීමෙන් ප්ලාස්ටික් thick න කොටස ඇති විය හැකි අතර එය ගිලීමේ සලකුණක් ඇති කිරීමට සහ සිසිලන කාලය වැඩි කිරීමට ඉඩ ඇති බැවින් එය සුදුසු නොවේ. සටහනේ පෙන්වා ඇති පරිදි ලොක්කා ඉළ ඇටයක් හරහා පැති බිත්තියට සම්බන්ධ කිරීමෙන් මෙම ගැටළුව විසඳා ගත හැකිය. සමනළ ඉළ ඇට ලබා දීමෙන් ලොක්කා දෘඩ කළ හැකිය.
තවත් කොටසක් සවි කිරීම සඳහා ලොක්කා මත ඉස්කුරුප්පු භාවිතා කරයි. නූල් සාදන ආකාරයේ ඉස්කුරුප්පු සහ පාගා දැමීමේ ඉස්කුරුප්පු වර්ග තිබේ. නූල් සාදන ඉස්කුරුප්පු තාප ස්ථායීකරණයේ ද නූල් කැපීමේ ඉස්කුරුප්පු අනිත්ය තාප ස්ථායී ප්ලාස්ටික් කොටස් සඳහා ද යොදා ගනී.
නූල් සාදන ඉස්කුරුප්පු මගින් සීතල ප්රවාහයෙන් ලොක්කාගේ අභ්යන්තර බිත්තියේ ගැහැණු කෙඳි නිපදවයි - ප්ලාස්ටික් කැපීමට වඩා දේශීයව විකෘති වී ඇත.
ඉස්කුරුප්පු ඇණ ඇතුළු කිරීමේ බලවේගයන්ට සහ සේවයේ ඉස්කුරුප්පු ඇණ මත තබා ඇති බරට ඔරොත්තු දීම සඳහා ඉස්කුරුප්පු ලොක්කා නිසි මානයන් තිබිය යුතුය.
නූල් ඉවත් කිරීමට හා ඉස්කුරුප්පු ඇරීමට ප්රතිරෝධය දැක්වීම සඳහා ඉස්කුරුප්පු ඇණට සාපේක්ෂව සිදුරේ ප්රමාණය ඉතා වැදගත් වේ.
ලොස් පිටත විෂ්කම්භය නිසා නූල් සෑදීම නිසා වළලු ආතතියට ඔරොත්තු දීමට තරම් විශාල විය යුතුය.
කෙටි දිගක් සඳහා පිවිසුම් විවේකයේදී බෝර් තරමක් විශාල විෂ්කම්භයක් ඇත. රිය පැදවීමට පෙර ඉස්කුරුප්පු ඇණ සොයා ගැනීමට මෙය උපකාරී වේ. එය ලොක්කාගේ විවෘත කෙළවරේ ආතතිය අඩු කරයි.
පොලිමර් නිෂ්පාදකයින් ඔවුන්ගේ ද්රව්ය සඳහා ලොක්කාගේ මානය තීරණය කිරීම සඳහා මාර්ගෝපදේශ ලබා දේ. ඉස්කුරුප්පු නිෂ්පාදකයින් විසින් ඉස්කුරුප්පු ඇණ සඳහා නිවැරදි සිදුරු ප්රමාණය සඳහා මාර්ගෝපදේශ ලබා දේ.
ලොක්කාගේ ඉස්කුරුප්පු ඇණ වටා ශක්තිමත් වෑල්ඩින් සන්ධි ඇතිවීම සහතික කළ යුතුය.
ආක්රමණශීලී පරිසරය යටතේ එය අසාර්ථක විය හැකි බැවින් ලොක්කා තුළ ඇති වන ආතතිය වළක්වා ගැනීමට සැලකිලිමත් විය යුතුය.
ලොක්කාගේ සිදුර නූල් ගැඹුරට වඩා ගැඹුරු විය යුතුය.
10. මතුපිට සැරසිලි
සමහර විට, හොඳ පෙනුමක් ලබා ගැනීම සඳහා, අපි බොහෝ විට ප්ලාස්ටික් නඩුවේ මතුපිට විශේෂ ප්රතිකාර කරන්නෙමු.
වයනය, ඉහළ ග්ලෙන්සි, ඉසින පින්තාරු කිරීම, ලේසර් කැටයම්, උණුසුම් මුද්දර දැමීම, විද්යුත් විච්ඡේදනය සහ යනාදිය. නිෂ්පාදනයේ සැලසුම කල්තියාම සැලකිල්ලට ගැනීම අවශ්ය වේ, පසුකාලීන සැකසුම් සාක්ෂාත් කරගත නොහැකි වීම හෝ නිෂ්පාදන එකලස් කිරීම කෙරෙහි බලපාන ප්රමාණයේ වෙනස්කම්.